Fasteners and Machining: Integrating Precision and Strength in Production
Fasteners and Machining: Integrating Precision and Strength in Production
Blog Article
Browsing the Globe of Fasteners and Machining: Techniques for Accuracy and Speed
In the detailed world of bolts and machining, the quest for precision and rate is a continuous difficulty that requires meticulous focus to detail and calculated preparation. From understanding the diverse variety of bolt types to choosing optimal products that can hold up against rigorous demands, each action in the procedure plays a critical function in attaining the desired result. Accuracy machining methods additionally elevate the complexity of this craft, needing a fragile equilibrium between technological knowledge and innovative methods. As we dive into the approaches that can boost both speed and efficiency in this domain, the interplay between high quality control procedures and functional excellence emerges as a critical centerpiece.
Understanding Fastener Types
When picking fasteners for a job, recognizing the various kinds available is vital for making sure optimum performance and dependability. Screws are used with nuts to hold products with each other, while screws are versatile fasteners that can be made use of with or without a nut, depending on the application. Washers are essential for distributing the lots of the bolt and preventing damage to the product being attached.
Selecting the Right Products
Comprehending the relevance of selecting the best products is extremely important in ensuring the ideal efficiency and integrity of the selected fastener kinds discussed previously. When it comes to fasteners and machining applications, the product choice plays an important function in establishing the total strength, resilience, rust resistance, and compatibility with the designated atmosphere. Different materials supply differing residential properties that can substantially affect the efficiency of the fasteners.
Typical products used for fasteners consist of steel, stainless-steel, brass, aluminum, and titanium, each having its one-of-a-kind toughness and weak points. Steel is renowned for its high toughness and longevity, making it ideal for a wide variety of applications. Stainless steel uses exceptional rust resistance, suitable for environments vulnerable to moisture and chemicals. Light weight aluminum is corrosion-resistant and lightweight, making it suitable for applications where weight decrease is critical. Brass is usually selected for its aesthetic allure and superb conductivity. Titanium is understood for its extraordinary strength-to-weight ratio, making it ideal for high-performance applications. Picking the ideal material entails thinking about factors such as toughness demands, environmental problems, and spending plan constraints to make certain the preferred performance and long life of the fasteners.
Accuracy Machining Techniques

Along with CNC machining, various other precision methods like grinding, turning, milling, and boring play crucial roles in fastener manufacturing. Grinding helps accomplish great surface coatings and tight dimensional tolerances, while turning is often utilized to develop cylindrical elements with exact sizes. Milling and drilling operations are vital for forming and producing openings in bolts, guaranteeing they meet precise requirements and feature correctly.
Enhancing Speed and Effectiveness
To optimize bolt production procedures, it is crucial to streamline procedures and carry out reliable strategies that match precision machining techniques. Automated systems can deal with repetitive jobs with precision and rate, enabling workers to focus on even more complicated and value-added tasks. By integrating these approaches, producers can attain a balance between rate and accuracy, eventually boosting their affordable edge in the fastener market.
High Quality Control Steps
Implementing extensive top quality control steps is critical in ensuring the dependability and uniformity of bolt products in the manufacturing process. Quality assurance actions encompass different stages, beginning with the selection of raw materials to the final find out here now assessment of the ended up bolts. One fundamental element of quality assurance is performing extensive product examinations to verify compliance with specifications. This includes evaluating aspects such as product make-up, longevity, and toughness to ensure that the fasteners meet industry standards. In addition, keeping an eye on the machining refines is vital to support dimensional accuracy and surface area coating high quality. Using advanced technology, such as computerized assessment systems and accuracy measuring devices, can improve the accuracy and efficiency of top quality control treatments.
Routine calibration of tools and machinery is crucial to preserve uniformity in production and make certain that fasteners satisfy the needed tolerances. Applying strict procedures for recognizing and addressing flaws or non-conformities is essential in preventing substandard products from going into the marketplace. By developing a comprehensive high quality control structure, manufacturers can support the online reputation of their brand and provide bolts that meet the highest standards of performance and toughness.
Verdict
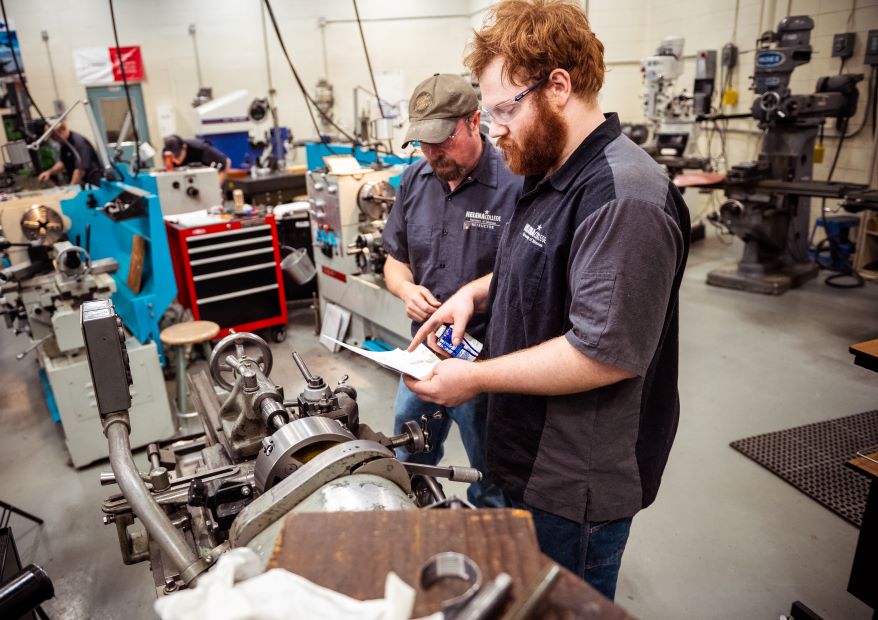
In the complex world of bolts and machining, the mission for precision and speed is a perpetual obstacle that demands precise interest to detail and tactical planning. When it comes to bolts and machining applications, the product choice plays a critical duty in determining the overall toughness, durability, corrosion resistance, and compatibility with the desired setting. Accuracy machining involves various sophisticated techniques that make sure the limited tolerances and requirements needed for bolts.In enhancement to CNC Go Here machining, other accuracy strategies like grinding, transforming, milling, and drilling play essential duties in fastener production.To maximize fastener production procedures, it is crucial to simplify operations and implement reliable methods that complement accuracy machining methods.
Report this page